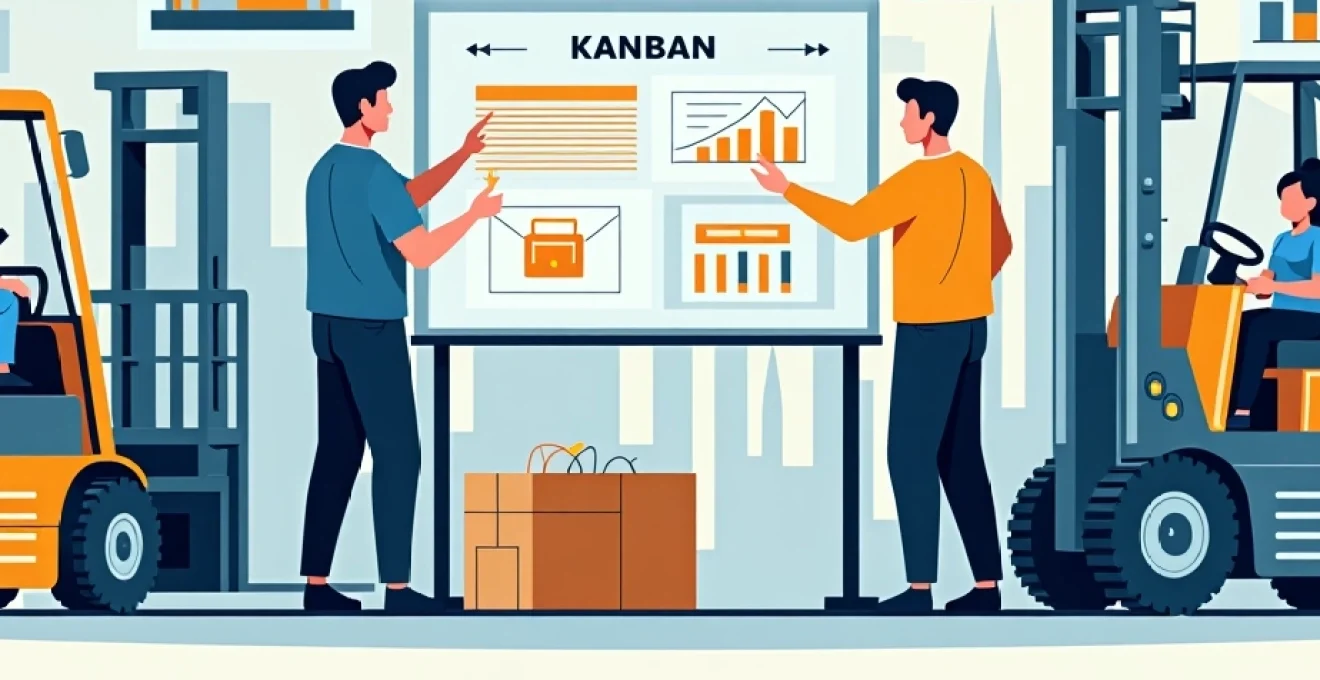
In der heutigen wettbewerbsintensiven Geschäftswelt ist die Optimierung der Produktionskette ein entscheidender Faktor für den Unternehmenserfolg. Eine effiziente Produktionskette ermöglicht es Unternehmen, Kosten zu senken, die Qualität zu verbessern und schneller auf Marktveränderungen zu reagieren. Durch den Einsatz moderner Methoden und Technologien können Unternehmen ihre Prozesse streamlinen, Verschwendung reduzieren und die Produktivität steigern. Von Lean-Manufacturing-Prinzipien bis hin zu digitalen Technologien der Industrie 4.0 gibt es zahlreiche Ansätze, um die Effizienz in der Produktion nachhaltig zu optimieren.
Analyse der Produktionskette mit Wertstrommanagement
Das Wertstrommanagement ist ein leistungsstarkes Werkzeug zur Analyse und Optimierung der Produktionskette. Es visualisiert den gesamten Produktionsablauf von der Bestellung bis zur Auslieferung und macht Verschwendung sowie Verbesserungspotenziale sichtbar. Durch die detaillierte Darstellung von Material- und Informationsflüssen können Unternehmen Engpässe identifizieren, nicht-wertschöpfende Aktivitäten eliminieren und den Gesamtprozess optimieren.
Ein wichtiger Schritt bei der Wertstromanalyse ist die Erfassung der Ist-Situation. Hierbei werden alle Prozessschritte, Lagerbestände, Durchlaufzeiten und Informationsflüsse dokumentiert. Anschließend wird ein Soll-Zustand definiert, der einen optimierten Wertstrom darstellt. Der Vergleich zwischen Ist- und Soll-Zustand offenbart Verbesserungspotenziale und bildet die Grundlage für konkrete Optimierungsmaßnahmen.
Die Implementierung des optimierten Wertstroms erfolgt schrittweise und unter Einbeziehung aller beteiligten Mitarbeiter. Durch regelmäßige Überprüfung und Anpassung wird sichergestellt, dass die Verbesserungen nachhaltig sind und sich die Produktionskette kontinuierlich weiterentwickelt. Das Wertstrommanagement schafft so die Basis für eine schlanke und effiziente Produktion .
Implementierung von Lean-Manufacturing-Prinzipien
Lean Manufacturing ist ein ganzheitlicher Ansatz zur Optimierung der Produktionskette, der auf die Eliminierung von Verschwendung und die Steigerung der Wertschöpfung abzielt. Die Implementierung von Lean-Prinzipien kann zu erheblichen Effizienzsteigerungen führen und die Wettbewerbsfähigkeit von Unternehmen nachhaltig verbessern. Im Kern geht es darum, alle Aktivitäten, die keinen Mehrwert für den Kunden schaffen, zu identifizieren und zu beseitigen.
Just-in-Time-Produktion und Kanban-Systeme
Just-in-Time (JIT) ist ein Kernprinzip des Lean Manufacturing, das darauf abzielt, Produkte genau zum benötigten Zeitpunkt in der erforderlichen Menge zu produzieren. Durch die Reduzierung von Lagerbeständen und Zwischenprodukten werden Kapitalbindung und Durchlaufzeiten minimiert. Kanban-Systeme unterstützen die JIT-Produktion, indem sie den Materialfluss steuern und eine bedarfsgerechte Produktion ermöglichen.
Die Einführung von JIT und Kanban erfordert eine genaue Planung und enge Abstimmung mit Zulieferern. Unternehmen müssen ihre Prozesse flexibilisieren und Lieferketten optimieren, um auf Nachfrageschwankungen reagieren zu können. Der Einsatz von digitalen Kanban-Boards kann die Implementierung erleichtern und die Transparenz in der Produktion erhöhen.
5S-Methode zur Arbeitsplatzorganisation
Die 5S-Methode ist ein systematischer Ansatz zur Arbeitsplatzorganisation, der die Effizienz und Qualität in der Produktion steigert. Die fünf S stehen für Sortieren, Systematisieren, Säubern, Standardisieren und Selbstdisziplin. Durch die konsequente Anwendung dieser Prinzipien werden Arbeitsplätze optimiert, Suchzeiten reduziert und die Arbeitssicherheit erhöht.
Bei der Umsetzung der 5S-Methode ist es wichtig, alle Mitarbeiter einzubeziehen und eine Kultur der kontinuierlichen Verbesserung zu etablieren. Regelmäßige Audits und Schulungen helfen, die Standards aufrechtzuerhalten und weiterzuentwickeln. Die 5S-Methode legt den Grundstein für weitere Lean-Initiativen und schafft eine visuelle Kontrolle in der Produktion.
Kaizen für kontinuierliche Verbesserung
Kaizen, das japanische Wort für "Verbesserung", steht für einen kontinuierlichen Verbesserungsprozess, der alle Mitarbeiter einbezieht. Ziel ist es, durch viele kleine Verbesserungsschritte die Gesamteffizienz der Produktion stetig zu erhöhen. Kaizen fördert eine Kultur, in der jeder Mitarbeiter ermutigt wird, Verbesserungsvorschläge einzubringen und umzusetzen.
Die Implementierung von Kaizen erfordert ein Umdenken in der Unternehmenskultur. Führungskräfte müssen offen für Vorschläge sein und Mitarbeiter aktiv in Verbesserungsprozesse einbinden. Kaizen-Events oder Workshops können genutzt werden, um gezielt an spezifischen Problemen zu arbeiten und schnelle Verbesserungen zu erzielen. Durch die kontinuierliche Anwendung von Kaizen können Unternehmen ihre Wettbewerbsfähigkeit langfristig sichern .
Six Sigma zur Fehlervermeidung
Six Sigma ist eine datengetriebene Methode zur Qualitätsverbesserung und Fehlervermeidung in der Produktion. Das Ziel ist es, Prozesse so zu optimieren, dass sie nahezu fehlerfrei ablaufen. Six Sigma nutzt statistische Methoden, um Prozessvariationen zu reduzieren und die Qualität zu verbessern. Die Methode basiert auf dem DMAIC-Zyklus: Define, Measure, Analyze, Improve und Control.
Die Implementierung von Six Sigma erfordert geschulte Experten, sogenannte Green Belts und Black Belts, die Projekte zur Prozessverbesserung leiten. Durch die systematische Analyse von Daten können Unternehmen die Ursachen von Qualitätsproblemen identifizieren und gezielt beheben. Six Sigma kann zu erheblichen Kosteneinsparungen führen, indem es Ausschuss und Nacharbeiten minimiert .
Digitalisierung und Industrie 4.0 in der Produktion
Die Digitalisierung und die Konzepte der Industrie 4.0 revolutionieren die Produktionslandschaft. Durch die Integration von intelligenten Systemen, Sensoren und Datenanalyse können Unternehmen ihre Produktionsprozesse auf ein neues Effizienzniveau heben. Die Vernetzung von Maschinen und Systemen ermöglicht eine flexible und adaptive Produktion, die schnell auf Marktveränderungen reagieren kann.
Einsatz von Manufacturing Execution Systems (MES)
Manufacturing Execution Systems (MES) sind Softwarelösungen, die die Planung, Steuerung und Überwachung von Produktionsprozessen in Echtzeit ermöglichen. Sie bilden die Schnittstelle zwischen den Planungssystemen (ERP) und der Produktionsebene. MES sammeln Daten aus verschiedenen Quellen und liefern wichtige Informationen für Entscheidungsträger.
Durch den Einsatz von MES können Unternehmen ihre Produktionsabläufe transparenter gestalten und Ineffizienzen schneller erkennen. Die Systeme ermöglichen eine dynamische Produktionsplanung und -steuerung, was zu einer höheren Auslastung der Anlagen und kürzeren Durchlaufzeiten führt. MES unterstützen auch die Qualitätssicherung und Rückverfolgbarkeit von Produkten.
Predictive Maintenance durch IoT-Sensoren
Predictive Maintenance nutzt IoT-Sensoren und Datenanalyse, um den Zustand von Maschinen und Anlagen kontinuierlich zu überwachen und potenzielle Ausfälle vorherzusagen. Durch die frühzeitige Erkennung von Verschleiß oder Anomalien können Wartungsarbeiten gezielt geplant und ungeplante Stillstandzeiten minimiert werden. Dies führt zu einer höheren Anlagenverfügbarkeit und reduziert Wartungskosten.
Die Implementierung von Predictive Maintenance erfordert die Installation von Sensoren an kritischen Komponenten sowie die Entwicklung von Algorithmen zur Datenanalyse. Unternehmen müssen in die entsprechende Infrastruktur und Fachkräfte investieren, um die Vorteile voll auszuschöpfen. Langfristig kann Predictive Maintenance zu einer signifikanten Steigerung der Gesamtanlageneffektivität (OEE) führen.
Datenanalyse mit Machine Learning Algorithmen
Machine Learning Algorithmen ermöglichen es, große Datenmengen aus der Produktion zu analysieren und wertvolle Erkenntnisse zu gewinnen. Durch die Anwendung von künstlicher Intelligenz können Muster erkannt, Prognosen erstellt und Optimierungspotenziale identifiziert werden. Dies führt zu einer datengetriebenen Entscheidungsfindung in der Produktion.
Die Implementierung von Machine Learning in der Produktion erfordert eine solide Datenbasis und entsprechende Fachkompetenz. Unternehmen müssen in die Datenerfassung und -qualität investieren sowie Data Scientists einbinden, um die Algorithmen zu entwickeln und zu trainieren. Der Einsatz von Machine Learning kann zu signifikanten Effizienzsteigerungen in Bereichen wie Qualitätskontrolle, Bestandsmanagement und Produktionsplanung führen.
Augmented Reality für Prozessoptimierung
Augmented Reality (AR) bietet neue Möglichkeiten zur Optimierung von Produktionsprozessen. Durch die Einblendung virtueller Informationen in das Sichtfeld der Mitarbeiter können komplexe Arbeitsabläufe vereinfacht und Fehler reduziert werden. AR-Systeme unterstützen bei der Montage, Wartung und Qualitätskontrolle, indem sie kontextbezogene Informationen und Anleitungen in Echtzeit bereitstellen.
Die Einführung von AR-Technologien erfordert die Entwicklung spezifischer Anwendungen und die Integration in bestehende IT-Systeme. Mitarbeiter müssen im Umgang mit AR-Geräten geschult werden, um die Vorteile voll auszuschöpfen. Langfristig kann AR zu einer Steigerung der Produktivität und Qualität in der Produktion führen.
Optimierung der Lieferkette und Logistik
Eine effiziente Produktionskette hängt maßgeblich von einer optimierten Lieferkette und Logistik ab. Durch die Verbesserung der Materialflüsse, die Reduzierung von Lagerbeständen und die Optimierung der Transportwege können Unternehmen erhebliche Kosteneinsparungen erzielen und ihre Reaktionsfähigkeit erhöhen. Die Integration von Lieferanten und Kunden in die Planung ist dabei von entscheidender Bedeutung.
Moderne Supply Chain Management Systeme ermöglichen eine ganzheitliche Steuerung der Lieferkette . Durch Echtzeitdaten und Prognosemodelle können Unternehmen ihre Bestände optimieren und Just-in-Time-Lieferungen realisieren. Die Nutzung von Track & Trace
-Technologien erhöht die Transparenz in der Lieferkette und ermöglicht eine proaktive Steuerung bei Störungen.
Ein weiterer wichtiger Aspekt ist die Optimierung der innerbetrieblichen Logistik. Durch den Einsatz von automatisierten Transportsystemen, wie fahrerlosen Transportsystemen (FTS) oder Förderbändern, können Materialflüsse effizienter gestaltet werden. Die Implementierung von Lean-Logistik-Konzepten, wie Milkrun-Systemen, trägt zur Reduzierung von Verschwendung und zur Verbesserung der Materialbereitstellung bei.
Qualitätsmanagement und Zertifizierungen
Ein effektives Qualitätsmanagement ist unerlässlich für die Optimierung der Produktionskette. Es stellt sicher, dass Produkte und Prozesse den definierten Anforderungen entsprechen und kontinuierlich verbessert werden. Zertifizierungen nach international anerkannten Standards demonstrieren die Einhaltung von Qualitätsstandards und können die Wettbewerbsfähigkeit erhöhen.
ISO 9001 Implementierung und Audits
Die ISO 9001 ist der weltweit anerkannte Standard für Qualitätsmanagementsysteme. Die Implementierung eines ISO 9001-konformen Systems hilft Unternehmen, ihre Prozesse zu standardisieren, die Kundenzufriedenheit zu erhöhen und eine Kultur der kontinuierlichen Verbesserung zu etablieren. Regelmäßige interne und externe Audits stellen sicher, dass das System aufrechterhalten und weiterentwickelt wird.
Die Einführung von ISO 9001 erfordert die Dokumentation aller qualitätsrelevanten Prozesse und die Schulung der Mitarbeiter. Ein prozessorientierter Ansatz hilft, Schnittstellen zu optimieren und Verantwortlichkeitenklar zu definieren. Die ISO 9001-Zertifizierung kann zu einer verbesserten Kundenzufriedenheit und höheren Effizienz in der Produktion führen.
Total Quality Management (TQM) Strategien
Total Quality Management (TQM) ist ein ganzheitlicher Ansatz zur Qualitätsverbesserung, der alle Mitarbeiter und Prozesse einbezieht. TQM zielt darauf ab, eine Qualitätskultur im gesamten Unternehmen zu etablieren und die Kundenzufriedenheit kontinuierlich zu steigern. Kernelemente von TQM sind Kundenorientierung, Prozessorientierung, kontinuierliche Verbesserung und die Einbeziehung aller Mitarbeiter.
Die Implementierung von TQM erfordert ein langfristiges Engagement des Managements und eine Veränderung der Unternehmenskultur. Unternehmen müssen Qualitätsziele definieren, Mitarbeiter schulen und Anreizsysteme schaffen, die qualitätsorientiertes Handeln fördern. TQM-Tools wie Qualitätszirkel, Fehlerursachenanalyse und Benchmarking unterstützen die systematische Verbesserung der Produktqualität.
Statistische Prozesskontrollen (SPC)
Statistische Prozesskontrollen (SPC) sind ein wichtiges Werkzeug zur Überwachung und Steuerung von Produktionsprozessen. Durch die Anwendung statistischer Methoden können Unternehmen Prozessvariationen erkennen, Trends analysieren und frühzeitig auf Abweichungen reagieren. SPC hilft dabei, die Prozessfähigkeit zu verbessern und die Anzahl fehlerhafter Produkte zu reduzieren.
Die Implementierung von SPC erfordert die Definition von Kontrollgrenzen, die Auswahl geeigneter Messmethoden und die Schulung der Mitarbeiter in der Interpretation von Kontrollkarten. Moderne SPC-Software ermöglicht eine Echtzeitüberwachung der Prozesse und automatische Alarmmeldungen bei Grenzwertüberschreitungen. Durch den konsequenten Einsatz von SPC können Unternehmen ihre Produktqualität verbessern und Kosten durch vermiedene Nacharbeiten und Ausschuss reduzieren.
Mitarbeiterqualifikation und Prozessverständnis
Die Optimierung der Produktionskette kann nur gelingen, wenn die Mitarbeiter über die notwendigen Qualifikationen verfügen und ein tiefes Verständnis der Prozesse haben. Kontinuierliche Weiterbildung und Schulungen sind entscheidend, um mit den technologischen Entwicklungen Schritt zu halten und die Effizienz in der Produktion zu steigern.
Ein effektives Skill-Management-System hilft Unternehmen, Kompetenzlücken zu identifizieren und gezielte Schulungsmaßnahmen zu planen. Cross-Training und Job-Rotation fördern die Flexibilität der Mitarbeiter und verbessern das Verständnis für die Zusammenhänge in der Produktion. Die Einführung von Lernfabriken oder Simulationsumgebungen ermöglicht es den Mitarbeitern, neue Methoden und Technologien in einer risikofreien Umgebung zu erproben.
Eine offene Kommunikationskultur und die aktive Einbindung der Mitarbeiter in Verbesserungsprozesse sind entscheidend für den Erfolg von Optimierungsmaßnahmen. Durch regelmäßige Feedbackrunden und Ideenwettbewerbe können wertvolle Vorschläge aus der Belegschaft gewonnen werden. Die Förderung von Eigenverantwortung und unternehmerischem Denken trägt dazu bei, dass Mitarbeiter proaktiv nach Möglichkeiten zur Effizienzsteigerung und Qualitätsverbesserung suchen.