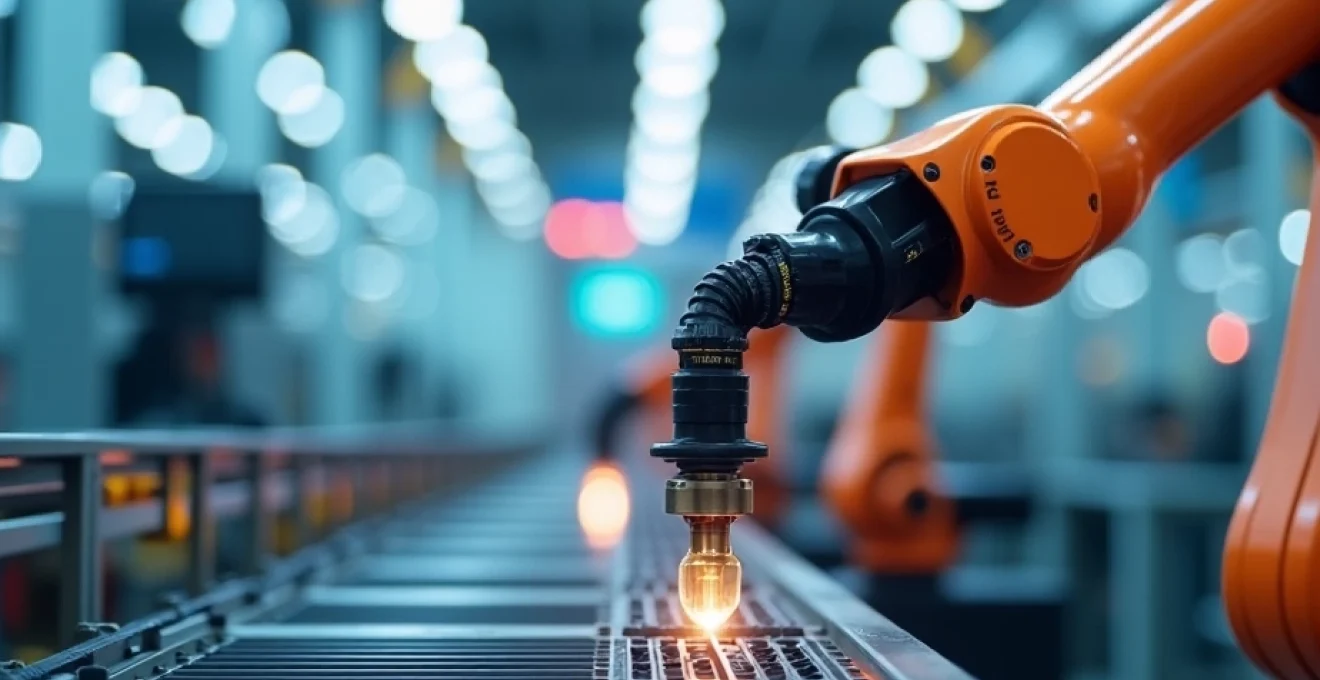
Die Fabrikautomatisierung erlebt derzeit eine Revolution. Innovative Technologien transformieren Produktionsprozesse, steigern die Effizienz und eröffnen völlig neue Möglichkeiten in der industriellen Fertigung. Von kollaborativen Robotern bis hin zu künstlicher Intelligenz - die Zukunft der Fabrikautomatisierung verspricht eine Ära der smarten, vernetzten und hochflexiblen Produktion. Doch welche Trends prägen aktuell die Branche und wie verändern sie die Art und Weise, wie Fabriken arbeiten?
Industrie 4.0 und die digitale Transformation in der Fertigung
Industrie 4.0 bildet das Fundament für die digitale Transformation der Fertigungsindustrie. Dieser Megatrend beschreibt die umfassende Digitalisierung und Vernetzung industrieller Prozesse. Durch die Integration von Informations- und Kommunikationstechnologien entstehen cyber-physische Systeme, die eine nahtlose Verbindung zwischen der physischen und der digitalen Welt herstellen.
Ein Kernaspekt von Industrie 4.0 ist die Schaffung intelligenter Fabriken. Diese zeichnen sich durch hohe Flexibilität, Ressourceneffizienz und Transparenz aus. Sensoren, Aktoren und autonome Systeme ermöglichen eine Echtzeitsteuerung der Produktion. Maschinen kommunizieren untereinander und mit den Produkten, wodurch sich Fertigungsprozesse selbst optimieren können.
Die Vorteile dieser digitalen Transformation sind vielfältig: Produktionsabläufe werden effizienter, die Qualität steigt und Kosten sinken. Gleichzeitig ermöglicht die erhöhte Flexibilität eine stärkere Individualisierung der Produktion - ein entscheidender Wettbewerbsvorteil in Zeiten zunehmender Kundenanforderungen.
Die intelligente Fabrik repräsentiert einen Paradigmenwechsel in der industriellen Produktion. Sie passt sich dynamisch an Marktanforderungen an und nutzt Daten, um kontinuierlich zu lernen und sich zu verbessern.
Um von den Möglichkeiten der Industrie 4.0 zu profitieren, müssen Unternehmen ihre bestehenden Systeme modernisieren und in neue Technologien investieren. Dies erfordert oft erhebliche finanzielle und personelle Ressourcen. Doch der Aufwand lohnt sich: Studien zeigen, dass Unternehmen, die konsequent auf Industrie 4.0-Technologien setzen, ihre Produktivität um bis zu 30% steigern können.
Fortschritte in der Robotik und kollaborative Roboter (Cobots)
Die Robotik hat in den letzten Jahren enorme Fortschritte gemacht. Moderne Industrieroboter sind präziser, schneller und vielseitiger als je zuvor. Doch der wohl bedeutendste Trend in diesem Bereich sind kollaborative Roboter, kurz Cobots. Diese neue Generation von Robotern ist speziell dafür konzipiert, sicher und effizient mit Menschen zusammenzuarbeiten.
Cobots zeichnen sich durch ihre Flexibilität, einfache Programmierbarkeit und fortschrittliche Sicherheitsfunktionen aus. Im Gegensatz zu traditionellen Industrierobotern benötigen sie keine Schutzzäune und können direkt neben menschlichen Mitarbeitern eingesetzt werden. Dies eröffnet völlig neue Möglichkeiten für die Mensch-Roboter-Kollaboration in der Produktion.
KUKA LBR iiwa: Flexibilität und Sicherheit in der Mensch-Roboter-Kollaboration
Der KUKA LBR iiwa (Leichtbauroboter - intelligent industrial work assistant) ist ein Paradebeispiel für moderne Cobot-Technologie. Mit seinen sieben Achsen und integrierten Momentensensoren in jedem Gelenk bietet er außergewöhnliche Flexibilität und Feingefühl. Der LBR iiwa kann selbst empfindliche Bauteile präzise handhaben und dabei sicher mit Menschen interagieren.
Ein besonderes Merkmal des LBR iiwa ist seine Nachgiebigkeit . Durch seine sensitiven Gelenke kann er auf externe Kräfte reagieren und seine Bewegungen entsprechend anpassen. Dies ermöglicht nicht nur eine sichere Zusammenarbeit mit Menschen, sondern auch komplexe Montageaufgaben, bei denen Feingefühl gefragt ist.
Universal Robots UR10e: Einsatz in KMUs und flexible Produktionslinien
Der UR10e von Universal Robots hat sich besonders in kleinen und mittleren Unternehmen (KMUs) etabliert. Mit einer Traglast von bis zu 10 kg und einer Reichweite von 1300 mm eignet er sich für eine Vielzahl von Anwendungen - von der Materialhandhabung bis zur Maschinenbestückung.
Ein Hauptvorteil des UR10e ist seine einfache Programmierung. Dank intuitiver Benutzeroberfläche und Teach-In-Funktion können selbst Mitarbeiter ohne Programmierkenntnisse den Roboter in kurzer Zeit für neue Aufgaben einrichten. Dies macht den UR10e zu einem idealen Werkzeug für flexible Produktionslinien, wo häufig wechselnde Aufgaben anfallen.
ABB YuMi: Präzision und Effizienz in der Kleinteilemontage
Der ABB YuMi ist ein kollaborativer Zweiarmroboter, der speziell für die Präzisionsmontage kleiner Teile entwickelt wurde. Mit seinen beiden Armen kann er komplexe Montageaufgaben ausführen, die bisher manuell erledigt werden mussten. Besonders in der Elektronikindustrie und bei der Herstellung von Präzisionsinstrumenten kommt der YuMi zum Einsatz.
Die Kameraführung und fortschrittliche Bildverarbeitungssoftware ermöglichen es dem YuMi, selbst kleinste Bauteile präzise zu erkennen und zu handhaben. Durch seine kompakte Bauweise und die inhärente Sicherheit kann er direkt neben menschlichen Mitarbeitern eingesetzt werden, was eine flexible Gestaltung von Montageprozessen erlaubt.
Fanuc CR-35iA: Schwerlasthandhabung mit Cobot-Technologie
Der Fanuc CR-35iA beweist, dass kollaborative Roboter auch für Schwerlastaufgaben geeignet sind. Mit einer Traglast von bis zu 35 kg ist er einer der stärksten Cobots auf dem Markt. Trotz seiner Kraft verfügt er über sensitive Sensoren, die eine sichere Zusammenarbeit mit Menschen ermöglichen.
Ein Einsatzgebiet des CR-35iA ist die ergonomische Unterstützung bei schweren Hebeaufgaben. Er kann Mitarbeiter bei der Handhabung schwerer Werkstücke unterstützen und so das Risiko von Verletzungen reduzieren. In der Automobilindustrie wird er beispielsweise für die Montage von Antriebssträngen oder das Handling von Karosserieteilen eingesetzt.
Die Entwicklung leistungsfähiger Cobots wie des CR-35iA zeigt, dass die Grenzen zwischen traditionellen Industrierobotern und kollaborativen Systemen zunehmend verschwimmen. Dies eröffnet neue Möglichkeiten für die flexible Gestaltung von Produktionsprozessen, bei denen Mensch und Maschine optimal zusammenarbeiten.
Künstliche Intelligenz und Machine Learning in der Prozessoptimierung
Künstliche Intelligenz (KI) und Machine Learning (ML) revolutionieren die Art und Weise, wie Fabriken arbeiten. Diese Technologien ermöglichen es, riesige Datenmengen zu analysieren, Muster zu erkennen und daraus Handlungsempfehlungen abzuleiten. In der Fabrikautomatisierung finden KI und ML vielfältige Anwendungen - von der Prozessoptimierung bis zur vorausschauenden Wartung.
Predictive Maintenance mit IBM Watson IoT Platform
Die IBM Watson IoT Platform ist ein leistungsstarkes Tool für die Implementierung von Predictive Maintenance-Lösungen. Durch die Analyse von Sensordaten kann Watson frühzeitig Anomalien erkennen und potenzielle Maschinenausfälle vorhersagen. Dies ermöglicht eine proaktive Wartung, bevor es zu kostspieligen Produktionsunterbrechungen kommt.
Ein Beispiel für den erfolgreichen Einsatz von Watson ist die Zusammenarbeit mit dem Aufzugshersteller KONE. Durch die kontinuierliche Überwachung von Aufzugsystemen konnte die Ausfallrate signifikant reduziert werden. Die KI-gestützte Analyse ermöglicht es, den optimalen Zeitpunkt für Wartungsarbeiten zu bestimmen und so die Verfügbarkeit der Anlagen zu maximieren.
Siemens MindSphere: KI-gestützte Datenanalyse für Produktionseffizienz
Siemens MindSphere ist eine Cloud-basierte IoT-Plattform, die KI-Technologien nutzt, um Produktionsprozesse zu optimieren. Durch die Analyse von Maschinendaten, Produktionsparametern und Qualitätsdaten können Ineffizienzen aufgedeckt und Verbesserungspotenziale identifiziert werden.
Ein konkreter Anwendungsfall ist die Energieoptimierung in Produktionsanlagen. MindSphere analysiert den Energieverbrauch einzelner Maschinen und Prozesse und schlägt Maßnahmen zur Effizienzsteigerung vor. In einigen Fällen konnten Unternehmen ihren Energieverbrauch um bis zu 30% reduzieren.
Google Cloud AI Platform: Automatisierte Qualitätskontrolle in Echtzeit
Die Google Cloud AI Platform bietet leistungsfähige Tools für die Implementierung von Machine Learning-Lösungen in der Fertigung. Ein bedeutendes Anwendungsgebiet ist die automatisierte Qualitätskontrolle mittels Bildverarbeitung und Deep Learning.
Durch den Einsatz von neuronalen Netzen können selbst kleinste Defekte in Hochgeschwindigkeit erkannt werden. Dies ermöglicht eine 100%ige Qualitätskontrolle in Echtzeit, was mit herkömmlichen Methoden oft nicht realisierbar ist. Unternehmen wie der Automobilzulieferer Continental nutzen diese Technologie bereits erfolgreich zur Inspektion von Reifenprofilen.
Die Integration von KI und ML in die Fabrikautomatisierung stellt Unternehmen vor neue Herausforderungen. Es bedarf spezifischer Expertise und oft erheblicher Investitionen in Infrastruktur und Datenmanagement. Doch die Potenziale sind enorm: Studien zeigen, dass der Einsatz von KI in der Fertigung die Produktivität um bis zu 40% steigern kann.
Fortschrittliche Sensorik und Industrial Internet of Things (IIoT)
Das Industrial Internet of Things (IIoT) bildet das Rückgrat der modernen Fabrikautomatisierung. Durch die Vernetzung von Maschinen, Sensoren und Steuerungssystemen entsteht ein digitales Abbild der Produktion, das neue Möglichkeiten für Optimierung und Kontrolle eröffnet. Fortschrittliche Sensortechnologien spielen dabei eine Schlüsselrolle.
SICK AG: Intelligente Sensoren für Industrie 4.0-Anwendungen
Die SICK AG ist führend in der Entwicklung intelligenter Sensoren für industrielle Anwendungen. Ihre Produkte reichen von einfachen Präsenzsensoren bis hin zu komplexen 3D-Vision-Systemen. Ein Beispiel ist der Inspector PIM60
- ein intelligenter Kamerasensor, der Bildverarbeitung und Auswertung direkt im Gerät durchführt.
Diese Edge Computing -Fähigkeit ermöglicht schnelle Reaktionszeiten und reduziert die Datenübertragung zum zentralen Steuerungssystem. In der Praxis wird der Inspector PIM60 beispielsweise zur Qualitätskontrolle in der Verpackungsindustrie eingesetzt, wo er Etiketten und Verschlüsse in Echtzeit überprüft.
Bosch Rexroth: IIoT-Lösungen für vernetzte Fertigungsumgebungen
Bosch Rexroth bietet umfassende IIoT-Lösungen für die vernetzte Fabrik. Die ActiveCockpit
-Plattform beispielsweise integriert Daten aus verschiedenen Quellen und visualisiert sie in Echtzeit. Dies ermöglicht eine transparente Darstellung von Produktionsprozessen und unterstützt datenbasierte Entscheidungen.
Ein besonderer Fokus liegt auf der Flexibilisierung der Produktion . Durch den Einsatz von RFID-Technologie und intelligenten Werkstückträgern können Produktionslinien schnell an wechselnde Anforderungen angepasst werden. Dies ist besonders in der Automobilindustrie relevant, wo zunehmend individuelle Kundenanforderungen berücksichtigt werden müssen.
Pepperl+Fuchs: Ultraschall- und RFID-Technologien in der Prozessautomatisierung
Pepperl+Fuchs hat sich auf Sensortechnologien für die Prozessautomatisierung spezialisiert. Ihre Ultraschallsensoren der Serie F77
zeichnen sich durch hohe Präzision und Robustheit aus. Sie werden beispielsweise in der Füllstandsmessung oder zur Positionserkennung in rauen Industrieumgebungen eingesetzt.
Im Bereich RFID bietet Pepperl+Fuchs Lösungen für die lückenlose Rückverfolgbarkeit von Produkten und Materialien in der Lieferkette. RFID-Tags ermöglichen eine präzise Verfolgung von Waren vom Rohmaterial bis zum Endprodukt. Dies verbessert nicht nur die Logistik, sondern unterstützt auch die Qualitätssicherung und Rückverfolgbarkeit.
Die Integration fortschrittlicher Sensorik und IIoT-Technologien in die Fabrikautomatisierung bietet enorme Potenziale. Unternehmen können ihre Prozesse transparenter gestalten, flexibler auf Marktanforderungen reagieren und die Effizienz ihrer Produktion steigern. Allerdings erfordert die Implementierung solcher Systeme oft erhebliche Investitionen und eine Anpassung bestehender IT-Infrastrukturen.
Additive Fertigung und 3D-Druck in der industriellen Produktion
Additive Fertigungsverfahren und 3D-Druck revolutionieren die Art und Weise, wie Produkte hergestellt werden. Diese Technologien ermöglichen die Produktion komplexer Geometrien, die mit konventionellen Methoden nicht oder nur schwer realisierbar sind. In der industriellen Fertigung finden sie zunehmend Anwendung - von der Prototypenerstellung bis zur Serienfertigung.
EOS M 400-4: Metall-3D-Druck für Großserienproduktion
Der EOS M 400-4 ist ein industrieller 3D-Drucker für die additive Fertigung von Metallteilen. Mit vier Lasern und einem großen Bauraum eignet er sich besonders für die Großserienproduktion. Die Multilaser-Technologie ermöglicht eine deutliche Steigerung der Produktivität im Vergleich zu Einzellaser-Systemen.
Ein Anwendungsbeispiel ist die Produktion von Turbinenkomponenten in der Luftfahrtindustrie. Durch die additive Fertigung können komplexe Kühlkanäle integriert werden, was die Effizienz der Turbinen erhöht. Gleichzeitig lässt sich das Gewicht der Bauteile reduzieren, was zu Treibstoffeinsparungen führt.
Stratasys F900: FDM-Technologie für funktionale Prototypen und Endprodukte
Der Stratasys F900 nutzt die FDM-Technologie (Fused Deposition Modeling) für die Herstellung großformatiger Kunststoffteile. Mit einem Bauraum von 914 x 610 x 914 mm eignet er sich besonders für die Produktion von Prototypen und Endprodukten in der Automobil- und Luftfahrtindustrie.
Ein besonderer Vorteil des F900 ist die Verarbeitung von Hochleistungskunststoffen wie ULTEM™ 9085. Dieses Material zeichnet sich durch hohe Festigkeit und Flammbeständigkeit aus, was es für Anwendungen in der Luftfahrt prädestiniert. Flugzeughersteller nutzen den F900 beispielsweise zur Produktion von Innenverkleidungen und Luftkanälen.
HP Multi Jet Fusion: Hochgeschwindigkeits-3D-Druck für Kunststoffteile
Die Multi Jet Fusion-Technologie von HP ermöglicht den 3D-Druck von Kunststoffteilen in bisher unerreichter Geschwindigkeit. Das System HP Jet Fusion 5200
kann bis zu 5000 Teile pro Woche produzieren, was es für die Serienfertigung interessant macht.
Ein Schlüsselmerkmal ist die gleichmäßige Materialverteilung über das gesamte Bauteil. Dies führt zu isotropen Eigenschaften, was die Vorhersagbarkeit und Zuverlässigkeit der Teile verbessert. In der Automobilindustrie wird die Technologie beispielsweise zur Produktion von Armaturenbrettelementen und Funktionsteilen eingesetzt.
Die Integration additiver Fertigungsverfahren in industrielle Produktionsprozesse stellt Unternehmen vor neue Herausforderungen. Es bedarf spezieller Expertise in der Konstruktion für additive Fertigung und oft einer Neugestaltung von Lieferketten. Doch die Potenziale sind enorm: Kürzere Produktionszeiten, Gewichtsreduzierung und die Möglichkeit zur Individualisierung machen 3D-Druck zu einer Schlüsseltechnologie für die Fabrik der Zukunft.
Digitale Zwillinge und virtuelle Inbetriebnahme
Digitale Zwillinge revolutionieren die Art und Weise, wie Produkte und Produktionssysteme entwickelt, getestet und optimiert werden. Sie ermöglichen eine virtuelle Repräsentation physischer Objekte oder Prozesse, die in Echtzeit aktualisiert wird. In Kombination mit der virtuellen Inbetriebnahme können Unternehmen Risiken minimieren und die Time-to-Market deutlich verkürzen.
Siemens Tecnomatix: Simulation und Optimierung von Produktionslinien
Siemens Tecnomatix ist eine umfassende Plattform für die digitale Fabrikplanung und -simulation. Mit Tools wie Plant Simulation
können komplette Produktionslinien virtuell abgebildet und optimiert werden. Dies ermöglicht es, verschiedene Szenarien durchzuspielen und die optimale Konfiguration zu finden, bevor auch nur eine einzige Maschine aufgestellt wird.
Ein konkreter Anwendungsfall ist die Durchsatzoptimierung in der Automobilfertigung. Durch die Simulation verschiedener Layoutvarianten und Produktionsstrategien können Engpässe identifiziert und beseitigt werden. In einigen Fällen konnten Unternehmen ihren Durchsatz um bis zu 20% steigern, ohne zusätzliche physische Ressourcen einzusetzen.
NVIDIA Omniverse: Echtzeit-Kollaboration in virtuellen Fabrikumgebungen
NVIDIA Omniverse ist eine Plattform für die Erstellung und den Betrieb von digitalen Zwillingen in Echtzeit. Sie ermöglicht die nahtlose Zusammenarbeit verschiedener Teams in einer photorealistischen 3D-Umgebung. In der Fabrikautomatisierung wird Omniverse für die virtuelle Planung und Optimierung von Produktionsanlagen eingesetzt.
Ein besonderes Merkmal ist die Physik-basierte Simulation. Roboterbewegungen, Materialeigenschaften und sogar Lichtverhältnisse können präzise simuliert werden. Dies ermöglicht eine realitätsnahe Erprobung von Produktionsabläufen und die frühzeitige Erkennung potenzieller Probleme.
Dassault Systèmes 3DEXPERIENCE: Ganzheitliche Plattform für digitale Zwillinge
Die 3DEXPERIENCE-Plattform von Dassault Systèmes bietet eine ganzheitliche Lösung für die Erstellung und Verwaltung digitaler Zwillinge. Sie integriert CAD, Simulation, Datenmanagement und Kollaborationstools in einer einzigen Umgebung. In der Fabrikautomatisierung wird sie für die End-to-End-Optimierung von Produkten und Produktionsprozessen eingesetzt.
Ein Anwendungsbeispiel ist die virtuelle Inbetriebnahme von Produktionsanlagen. Steuerungssysteme können an den digitalen Zwilling angeschlossen und unter realistischen Bedingungen getestet werden. Dies reduziert die Zeit für die physische Inbetriebnahme erheblich und minimiert das Risiko von Fehlern oder Verzögerungen.
Die Implementierung digitaler Zwillinge und virtueller Inbetriebnahme erfordert oft erhebliche Investitionen in Software und Infrastruktur. Zudem bedarf es spezialisierter Fachkräfte, die sowohl IT- als auch Produktions-Know-how mitbringen. Doch die Vorteile sind beträchtlich: Studien zeigen, dass Unternehmen durch den Einsatz digitaler Zwillinge ihre Entwicklungszeiten um bis zu 50% reduzieren und die Produktqualität signifikant verbessern können.
Die Fabrik der Zukunft existiert zunächst im digitalen Raum. Durch digitale Zwillinge und virtuelle Inbetriebnahme können wir Produktionssysteme optimieren, bevor der erste Spatenstich erfolgt.
Die hier vorgestellten Trends in der Fabrikautomatisierung zeigen deutlich: Die Zukunft der industriellen Produktion wird von Digitalisierung, Vernetzung und intelligenten Systemen geprägt sein. Unternehmen, die diese Technologien erfolgreich implementieren, können ihre Wettbewerbsfähigkeit deutlich steigern. Gleichzeitig stehen sie vor der Herausforderung, ihre Mitarbeiter für diese neue Ära der Produktion zu qualifizieren und eine Kultur der kontinuierlichen Innovation zu etablieren.