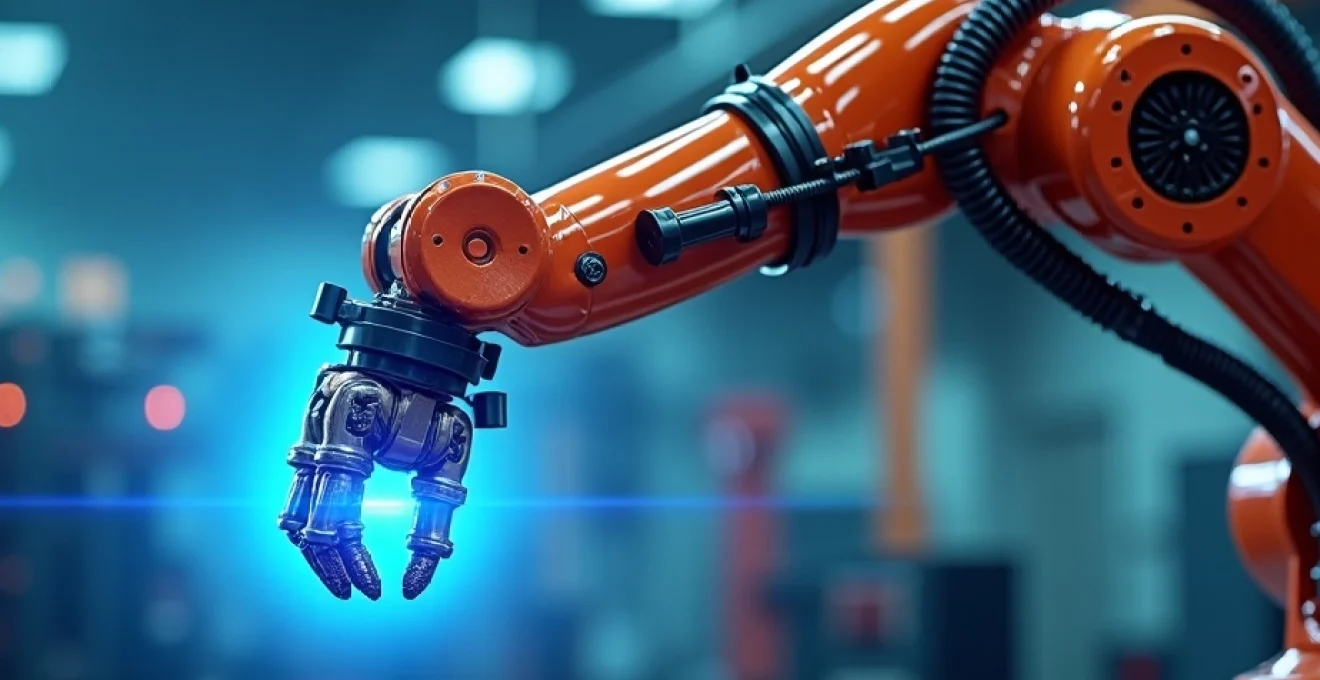
Industrieroboter haben sich zu unverzichtbaren Werkzeugen in der modernen Fertigungsindustrie entwickelt. Diese hochpräzisen Maschinen revolutionieren Produktionsprozesse, steigern die Effizienz und eröffnen neue Möglichkeiten für Innovation und Wettbewerbsfähigkeit. Von der Automobilbranche bis zur Pharmaindustrie verändern Industrieroboter die Art und Weise, wie Produkte hergestellt werden. Sie ermöglichen eine Präzision und Geschwindigkeit, die für Menschen unerreichbar ist, und arbeiten zuverlässig rund um die Uhr. Doch was macht diese Roboter so besonders, und warum sind sie der Schlüssel zur Zukunft der Fertigung?
Evolutionäre Entwicklung der Industrierobotik
Die Geschichte der Industrierobotik ist geprägt von kontinuierlicher Innovation und technologischem Fortschritt. Seit der Einführung des ersten Industrieroboters in den 1960er Jahren hat sich die Technologie rasant weiterentwickelt. Anfangs waren Roboter einfache, programmierbare Maschinen, die repetitive Aufgaben ausführten. Heute sind sie hochkomplexe Systeme, ausgestattet mit fortschrittlicher Sensorik, künstlicher Intelligenz und adaptiven Lernfähigkeiten.
Ein entscheidender Wendepunkt in der Evolution der Industrierobotik war die Integration von Computertechnologie und fortschrittlicher Steuerungssoftware. Dies ermöglichte eine deutlich präzisere Steuerung und flexiblere Programmierung der Roboter. In den 1980er und 1990er Jahren führte die Einführung von CAD/CAM-Systemen zu einer noch engeren Verzahnung von Konstruktion und Fertigung, was die Effizienz und Genauigkeit der robotergestützten Produktion weiter steigerte.
Mit dem Aufkommen der Industrie 4.0 und dem Internet der Dinge (IoT) hat die Industrierobotik einen weiteren Quantensprung gemacht. Moderne Roboter sind nicht mehr isolierte Einheiten, sondern vernetzte Systeme, die in Echtzeit mit anderen Maschinen und Produktionsprozessen kommunizieren können. Diese Vernetzung ermöglicht eine noch flexiblere und effizientere Produktion, die sich schnell an veränderte Marktanforderungen anpassen kann.
Die Evolution der Industrierobotik hat unsere Vorstellung von Produktionsmöglichkeiten grundlegend verändert und neue Maßstäbe in Bezug auf Präzision, Geschwindigkeit und Flexibilität gesetzt.
Kernkomponenten moderner Industrieroboter
Moderne Industrieroboter sind komplexe Systeme, die aus mehreren Kernkomponenten bestehen. Jede dieser Komponenten spielt eine entscheidende Rolle für die Leistungsfähigkeit und Präzision des Roboters. Lassen Sie uns einen genaueren Blick auf diese wichtigen Elemente werfen.
Hochpräzise Servomotoren und Aktuatoren
Das Herzstück eines jeden Industrieroboters sind seine Antriebe. Hochpräzise Servomotoren und Aktuatoren ermöglichen die genauen Bewegungen, die für komplexe Fertigungsaufgaben erforderlich sind. Diese Motoren zeichnen sich durch eine extrem hohe Positioniergenauigkeit aus, oft im Bereich von Mikrometern. Sie können schnell beschleunigen und abbremsen, was für effiziente Produktionszyklen unerlässlich ist.
Moderne Servomotoren sind zudem energieeffizient und können ihre Leistung an die jeweilige Aufgabe anpassen. Dies trägt nicht nur zur Reduzierung des Energieverbrauchs bei, sondern verlängert auch die Lebensdauer der Komponenten. Die Präzision dieser Antriebe wird durch fortschrittliche Encodersysteme unterstützt, die kontinuierlich die Position und Geschwindigkeit des Roboters überwachen und Abweichungen in Echtzeit korrigieren.
Fortschrittliche Sensorik und Bildverarbeitungssysteme
Ein weiterer entscheidender Faktor für die Leistungsfähigkeit moderner Industrieroboter ist ihre Fähigkeit, ihre Umgebung wahrzunehmen und darauf zu reagieren. Dies wird durch fortschrittliche Sensorik und Bildverarbeitungssysteme ermöglicht. Kraftsensoren erlauben es dem Roboter, den ausgeübten Druck präzise zu kontrollieren, was besonders bei empfindlichen Montageaufgaben wichtig ist.
Optische Sensoren und Kameras mit hochentwickelter Bildverarbeitungssoftware ermöglichen es dem Roboter, Objekte zu erkennen, zu lokalisieren und ihre Qualität zu überprüfen. Diese Systeme arbeiten oft mit künstlicher Intelligenz und maschinellem Lernen zusammen, um die Genauigkeit und Anpassungsfähigkeit weiter zu verbessern. So können Roboter beispielsweise Werkstücke in unterschiedlichen Positionen erkennen und greifen oder Qualitätskontrollen direkt während des Produktionsprozesses durchführen.
Leistungsfähige Steuerungssoftware und KI-Integration
Die Steuerungssoftware ist das Gehirn des Industrieroboters. Sie koordiniert alle Bewegungen und Aktionen des Roboters und integriert die Daten der verschiedenen Sensoren. Moderne Robotersteuerungen sind hochkomplexe Systeme, die in Echtzeit arbeiten und eine Vielzahl von Parametern gleichzeitig verarbeiten können.
Die Integration von künstlicher Intelligenz (KI) und maschinellem Lernen hat die Fähigkeiten von Industrierobotern nochmals deutlich erweitert. KI-Algorithmen ermöglichen es Robotern, aus Erfahrungen zu lernen und ihre Leistung kontinuierlich zu verbessern. Sie können Muster in Produktionsdaten erkennen, Anomalien frühzeitig identifizieren und sogar vorausschauende Wartung durchführen.
Ein besonders faszinierender Aspekt ist die Fähigkeit moderner Robotersysteme, komplexe Aufgaben durch Demonstration Learning zu erlernen. Hierbei führt ein menschlicher Operator die gewünschte Aufgabe einmal vor, und der Roboter kann diese dann selbstständig reproduzieren und optimieren. Diese Art des Lernens macht die Programmierung von Robotern deutlich einfacher und flexibler.
Robuste Mechanik und Leichtbaumaterialien
Die physische Struktur eines Industrieroboters muss höchsten Anforderungen an Präzision und Belastbarkeit genügen. Moderne Roboter kombinieren robuste Mechanik mit innovativen Leichtbaumaterialien, um maximale Stabilität bei minimaler Masse zu erreichen. Dies ermöglicht schnellere Bewegungen und reduziert den Energieverbrauch.
Fortschrittliche Materialien wie Kohlefaserverbundwerkstoffe oder spezielle Aluminiumlegierungen kommen zum Einsatz, um die Trägheit der beweglichen Teile zu reduzieren. Gleichzeitig müssen diese Materialien extremen Belastungen standhalten und über lange Zeit ihre Präzision bewahren. Hochpräzise Getriebe und Lagerungen sorgen für minimales Spiel und maximale Wiederholgenauigkeit, selbst bei tausendfacher Wiederholung der gleichen Bewegung.
Die Kombination aus hochpräzisen Antrieben, fortschrittlicher Sensorik, intelligenter Steuerung und robuster Mechanik macht moderne Industrieroboter zu wahren Meistern der Präzision und Effizienz.
Anwendungsfelder in der Fertigungsindustrie
Industrieroboter haben in nahezu allen Bereichen der Fertigungsindustrie Einzug gehalten. Ihre Vielseitigkeit und Anpassungsfähigkeit machen sie zu unverzichtbaren Werkzeugen in verschiedensten Produktionsumgebungen. Lassen Sie uns einige der wichtigsten Anwendungsfelder genauer betrachten.
Automobilindustrie: Schweißen und Lackieren mit KUKA-Robotern
Die Automobilindustrie war einer der ersten Sektoren, der Industrieroboter in großem Maßstab einsetzte, und sie bleibt bis heute einer der größten Anwender dieser Technologie. KUKA-Roboter spielen hier eine besonders wichtige Rolle, insbesondere beim Schweißen und Lackieren von Fahrzeugkarosserien.
Beim Schweißen erreichen KUKA-Roboter eine Präzision und Geschwindigkeit, die für menschliche Schweißer unerreichbar ist. Sie können komplexe Schweißnähte in Sekundenschnelle ausführen und dabei eine konstant hohe Qualität gewährleisten. Die Roboter sind in der Lage, verschiedene Schweißtechniken wie Punktschweißen, Lichtbogenschweißen oder Laserschweißen auszuführen und können sich flexibel an unterschiedliche Karosseriedesigns anpassen.
Im Bereich der Fahrzeuglackierung sorgen KUKA-Roboter für eine gleichmäßige und makellose Oberflächenqualität. Sie können Lacke präzise auftragen, ohne Tropfen oder Unebenheiten zu hinterlassen. Dank fortschrittlicher Sensorik und Steuerungssoftware passen sie sich automatisch an verschiedene Fahrzeugmodelle und Lackierungsspezifikationen an. Dies ermöglicht eine hohe Flexibilität in der Produktion bei gleichzeitig maximaler Effizienz und Qualität.
Elektronikindustrie: Präzisionsmontage durch ABB-Robotersysteme
In der Elektronikindustrie, wo Miniaturisierung und höchste Präzision gefragt sind, kommen häufig ABB-Robotersysteme zum Einsatz. Diese Roboter zeichnen sich durch ihre außergewöhnliche Genauigkeit und Geschwindigkeit bei der Montage kleinster Bauteile aus.
ABB-Roboter können winzige elektronische Komponenten wie Mikrochips oder SMD-Bauteile (Surface Mounted Devices) mit einer Genauigkeit von wenigen Mikrometern platzieren. Sie arbeiten dabei oft mit hochauflösenden Kamerasystemen zusammen, die jedes Bauteil vor der Montage prüfen und positionieren. Diese Kombination aus Robotik und Bildverarbeitung ermöglicht eine Qualitätskontrolle in Echtzeit und minimiert Fehler im Produktionsprozess.
Ein besonderes Merkmal der ABB-Roboter in der Elektronikindustrie ist ihre Fähigkeit zur flexiblen Anpassung an verschiedene Produktionslinien. Sie können schnell umprogrammiert werden, um neue Produkte oder Varianten zu fertigen, was besonders in der schnelllebigen Elektronikbranche von großem Vorteil ist.
Lebensmittelindustrie: Hygieneoptimierte Fanuc-Roboter
Die Lebensmittelindustrie stellt besondere Anforderungen an Industrieroboter, insbesondere in Bezug auf Hygiene und Reinigungsfähigkeit. Fanuc hat sich hier mit speziell entwickelten, hygieneoptimierte Robotern einen Namen gemacht.
Diese Roboter sind aus lebensmittelechten Materialien gefertigt und so konstruiert, dass sie leicht zu reinigen sind. Sie verfügen über glatte Oberflächen ohne Ecken und Kanten, in denen sich Schmutz oder Bakterien ansammeln könnten. Viele Modelle sind sogar wasserdicht und können mit Hochdruckreinigern gesäubert werden, was in der Lebensmittelindustrie oft erforderlich ist.
Fanuc-Roboter kommen in der Lebensmittelindustrie für verschiedenste Aufgaben zum Einsatz, von der Sortierung und Verpackung von Obst und Gemüse bis hin zur Handhabung von Fleisch- und Backwaren. Sie arbeiten präzise und schnell, ohne dabei die strengen Hygienevorschriften zu verletzen. Durch den Einsatz dieser Roboter können Lebensmittelhersteller nicht nur ihre Produktivität steigern, sondern auch die Lebensmittelsicherheit verbessern.
Pharmaindustrie: Reinraum-kompatible Yaskawa-Roboterlösungen
In der Pharmaindustrie, wo höchste Reinheit und Präzision gefordert sind, kommen oft Yaskawa-Roboter zum Einsatz. Diese Roboter sind speziell für den Einsatz in Reinräumen konzipiert und erfüllen die strengsten Anforderungen an Sauberkeit und Kontaminationsfreiheit.
Yaskawa-Roboter für die Pharmaindustrie sind so konstruiert, dass sie keine Partikel oder andere Verunreinigungen abgeben. Sie verfügen über spezielle Beschichtungen und Dichtungen, die verhindern, dass Schmiermittel oder andere Substanzen austreten können. Viele Modelle sind zudem für den Einsatz in sterilen Umgebungen zertifiziert und können sogar in Räumen der höchsten Reinheitsklasse arbeiten.
Diese Roboter übernehmen in der Pharmaindustrie vielfältige Aufgaben, von der präzisen Dosierung von Wirkstoffen bis hin zur Handhabung und Verpackung von Medikamenten. Sie gewährleisten dabei nicht nur höchste Präzision, sondern auch eine lückenlose Dokumentation aller Prozessschritte, was für die Qualitätssicherung und Rückverfolgbarkeit in der Pharmaindustrie von entscheidender Bedeutung ist.
Effizienzsteigerung durch Robotereinsatz
Der Einsatz von Industrierobotern führt zu einer signifikanten Steigerung der Effizienz in Produktionsprozessen. Diese Effizienzsteigerung lässt sich an mehreren Faktoren festmachen, die zusammen einen erheblichen Wettbewerbsvorteil für Unternehmen darstellen.
Zunächst einmal arbeiten Roboter mit einer Geschwindigkeit und Präzision, die für menschliche Arbeiter unerreichbar ist. Sie können komplexe Aufgaben in Sekundenschnelle ausführen und dabei eine gleichbleibende Qualität gewährleisten. Dies führt zu einer drastischen Reduzierung von Produktionszeiten und einer Erhöhung des Outputs.
Ein weiterer wichtiger Faktor ist die Verringerung von Fehlern und Ausschuss. Roboter arbeiten mit einer Präzision, die weit über dem liegt, was selbst erfahrene menschliche Arbeiter leisten können. Dies führt zu einer signifikanten Reduzierung von Materialverschwendung und Nacharbeiten, was wiederum Kosten spart und die Gesamteffizienz des Produktionsprozesses steigert.
Darüber hinaus können Roboter rund um die Uhr arbeiten, ohne Ermüdungserscheinungen oder Leistungsabfall. Dies ermöglicht einen kontinuierlichen Produktionsfluss und maximiert die Auslastung der Produktionsanlagen. In vielen Fällen kann durch den Einsatz von Robotern die Produktionskapazität verdoppelt oder sogar verdreifacht werden, ohne dass zusätzliche Schichten eingeführt werden müssen.
Ein oft übersehener Aspekt der Effizienzsteigerung durch Roboter ist die Verbesserung der Arbeitssicherheit. Roboter können gefährliche oder gesundheitsschädliche Aufgaben übernehmen, was die Zahl der Arbeitsunfälle und krankheitsbedingten Ausfälle reduziert. Dies führt nicht nur zu einer höheren Produktivität, sondern auch zu geringeren Kosten für Versicherungen und Kompensationszahlungen.
Der Einsatz von Industrierobotern ermöglicht eine Effizienzsteigerung, die weit über das hinausgeht, was durch konventionelle Optimierungsmethoden erreichbar ist. Sie sind der Schlüssel zur Wettbewerbsfähigkeit in einer globalisierten Wirtschaft.
Integration von Robotern in Industrie 4.0-Konzepte
Die Integration von Industrierobotern in Industrie 4.0-Konzepte markiert einen Paradigmenwechsel in der Fertigungsindustrie. Diese Verschmelzung von Robotik und digitalen Technologien eröffnet neue Möglichkeiten für Effizienz, Flexibilität und Innovation in der Produktion.
Vernetzung durch OPC UA und Industrial Ethernet
Eine Schlüsselkomponente der Integration von Robotern in Industrie 4.0-Umgebungen ist die Vernetzung durch standardisierte Kommunikationsprotokolle wie OPC UA (Open Platform Communications Unified Architecture) und Industrial Ethernet. Diese Protokolle ermöglichen eine nahtlose Kommunikation zwischen Robotern, Maschinen, Sensoren und übergeordneten Steuerungssystemen.
OPC UA bietet eine herstellerunabhängige, sichere und skalierbare Kommunikationsplattform, die es Robotern ermöglicht, Daten in Echtzeit auszutauschen und auf Veränderungen in der Produktionsumgebung zu reagieren. Industrial Ethernet-Protokolle wie PROFINET oder EtherCAT gewährleisten eine schnelle und zuverlässige Datenübertragung, die für die präzise Steuerung von Roboterbewegungen unerlässlich ist.
Durch diese Vernetzung können Roboter nicht nur untereinander kommunizieren, sondern auch mit anderen Systemen wie ERP (Enterprise Resource Planning) oder MES (Manufacturing Execution System) interagieren. Dies ermöglicht eine dynamische Anpassung der Produktion an Auftragsänderungen oder Materialverfügbarkeiten in Echtzeit.
Digitale Zwillinge für Robotersimulation und -optimierung
Digitale Zwillinge sind virtuelle Repräsentationen physischer Robotersysteme, die eine genaue Simulation und Optimierung von Produktionsprozessen ermöglichen. Diese digitalen Modelle erfassen alle relevanten Daten des realen Roboters, einschließlich seiner Geometrie, Kinematik und Betriebsparameter.
Mit Hilfe von digitalen Zwillingen können Ingenieure Roboterprozesse virtuell testen und optimieren, bevor sie in der realen Produktion implementiert werden. Dies reduziert Stillstandzeiten und minimiert das Risiko von Fehlern oder Kollisionen. Darüber hinaus ermöglichen digitale Zwillinge die kontinuierliche Optimierung von Roboterbewegungen und -pfaden, was zu einer Steigerung der Effizienz und Qualität führt.
Ein faszinierender Aspekt digitaler Zwillinge ist ihre Fähigkeit, Daten aus der realen Produktion zurück in die Simulation zu speisen. Dies ermöglicht ein kontinuierliches Lernen und Verbessern der Roboterprozesse, basierend auf tatsächlichen Betriebserfahrungen.
Predictive Maintenance mittels Roboter-Telemetrie
Predictive Maintenance, oder vorausschauende Wartung, ist ein weiterer Bereich, in dem die Integration von Robotern in Industrie 4.0-Konzepte große Vorteile bietet. Durch die kontinuierliche Überwachung von Roboter-Telemetriedaten können potenzielle Probleme frühzeitig erkannt und behoben werden, bevor sie zu Ausfällen führen.
Moderne Industrieroboter sind mit einer Vielzahl von Sensoren ausgestattet, die Daten über Temperatur, Vibration, Stromaufnahme und andere kritische Parameter in Echtzeit erfassen. Diese Daten werden analysiert, um Abweichungen vom Normalzustand zu erkennen und vorherzusagen, wann Wartungsarbeiten erforderlich sein werden.
Durch den Einsatz von künstlicher Intelligenz und maschinellem Lernen können diese Vorhersagemodelle kontinuierlich verbessert werden, was zu einer immer genaueren Wartungsplanung führt. Dies reduziert nicht nur ungeplante Ausfallzeiten, sondern optimiert auch die Wartungskosten, da Wartungsarbeiten nur dann durchgeführt werden, wenn sie tatsächlich erforderlich sind.
Flexible Produktionslinien durch mobile Roboterplattformen
Die Integration mobiler Roboterplattformen in Industrie 4.0-Konzepte eröffnet neue Möglichkeiten für flexible und adaptive Produktionslinien. Diese autonomen mobilen Roboter (AMR) können sich frei in der Produktionsumgebung bewegen und verschiedene Aufgaben an unterschiedlichen Stationen ausführen.
Mobile Roboterplattformen sind mit fortschrittlichen Navigationssystemen ausgestattet, die es ihnen ermöglichen, Hindernisse zu erkennen und zu umgehen. Sie können sich dynamisch an Veränderungen in der Produktionsumgebung anpassen und optimale Wege zwischen verschiedenen Arbeitsstationen finden.
Ein besonders innovativer Aspekt ist die Fähigkeit dieser Plattformen, sich selbstständig mit verschiedenen Werkzeugen oder Endeffektoren auszustatten. Dies ermöglicht einen schnellen Wechsel zwischen verschiedenen Produktionsaufgaben ohne menschliches Eingreifen. In Kombination mit cloudbasierten Produktionssteuerungssystemen können diese mobilen Roboter flexibel auf Änderungen in der Auftragslage oder Produktspezifikation reagieren.
Die Integration von Robotern in Industrie 4.0-Konzepte schafft intelligente, vernetzte Produktionsumgebungen, die sich kontinuierlich selbst optimieren und an veränderte Anforderungen anpassen können.
Herausforderungen und Zukunftsperspektiven der Industrierobotik
Trotz der vielen Vorteile und Fortschritte in der Industrierobotik gibt es nach wie vor Herausforderungen zu bewältigen. Gleichzeitig eröffnen sich faszinierende Zukunftsperspektiven, die das Potenzial haben, die Fertigungsindustrie weiter zu revolutionieren.
Eine der größten Herausforderungen bleibt die Programmierung und Bedienung von Robotersystemen. Obwohl moderne Roboter intuitiver zu bedienen sind als ihre Vorgänger, erfordert ihre effektive Nutzung nach wie vor spezialisiertes Fachwissen. Die Entwicklung von noch benutzerfreundlicheren Schnittstellen und Programmiermethoden, wie beispielsweise Programmierung durch Demonstration oder natürlichsprachliche Befehle, ist ein wichtiges Forschungsfeld.
Ein weiterer Aspekt ist die Frage der Sicherheit, insbesondere bei der Mensch-Roboter-Kollaboration. Während kollaborative Roboter bereits große Fortschritte in diesem Bereich gemacht haben, bleiben Fragen zur Langzeitsicherheit und zu komplexeren Interaktionsszenarien offen. Die Entwicklung noch fortschrittlicherer Sicherheitssysteme und -protokolle wird entscheidend sein, um das volle Potenzial der Mensch-Roboter-Zusammenarbeit auszuschöpfen.
In Bezug auf Zukunftsperspektiven zeichnen sich mehrere spannende Trends ab. Die weitere Integration von künstlicher Intelligenz und maschinellem Lernen wird Roboter noch adaptiver und autonomer machen. Wir können Systeme erwarten, die nicht nur vorprogrammierte Aufgaben ausführen, sondern eigenständig lernen und sich an neue Situationen anpassen können.
Die Entwicklung von Schwarmrobotersystemen, bei denen viele kleine, spezialisierte Roboter zusammenarbeiten, um komplexe Aufgaben zu bewältigen, ist ein weiteres vielversprechendes Forschungsgebiet. Diese Systeme könnten eine bisher unerreichte Flexibilität und Skalierbarkeit in der Produktion ermöglichen.
Schließlich wird die zunehmende Integration von Robotik mit anderen Zukunftstechnologien wie 3D-Druck, erweiterte Realität und Quantencomputing zu völlig neuen Fertigungsparadigmen führen. Wir stehen möglicherweise an der Schwelle zu einer Ära, in der Produktionsanlagen sich selbst entwerfen, optimieren und an veränderte Marktbedingungen anpassen können.