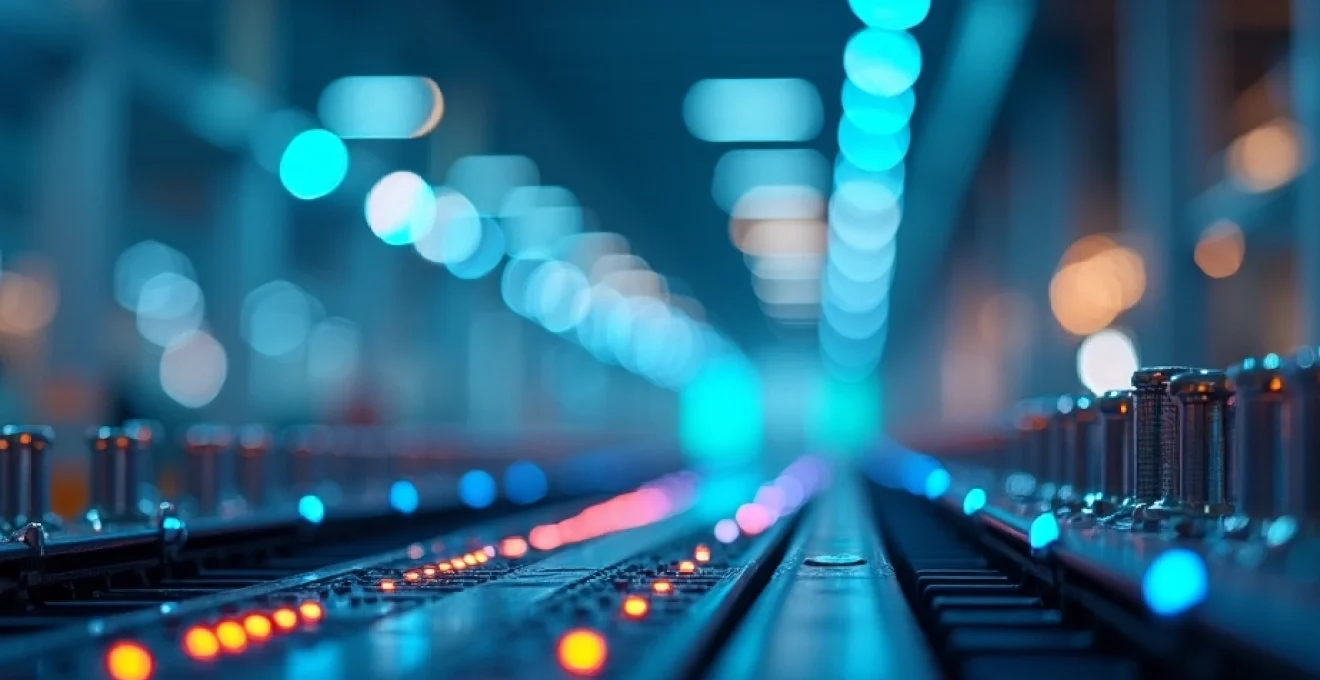
In der sich rasant entwickelnden Welt der Industrie 4.0 steht die Großproduktion vor beispiellosen Herausforderungen und Chancen. Künstliche Intelligenz (KI) hat sich als Schlüsseltechnologie für die Optimierung komplexer Fertigungsprozesse etabliert. Durch den Einsatz fortschrittlicher Algorithmen und Datenanalysen können Unternehmen ihre Produktionsabläufe revolutionieren, Effizienz steigern und Kosten senken. Diese Transformation verspricht nicht nur kurzfristige Gewinne, sondern auch langfristige Wettbewerbsvorteile in einem zunehmend digitalisierten Markt.
KI-gestützte Prozessoptimierung in der Industrie 4.0
Die Industrie 4.0 markiert einen Paradigmenwechsel in der Fertigungstechnologie. Durch die Integration von KI in Produktionsprozesse können Unternehmen ein beispielloses Maß an Automatisierung, Präzision und Anpassungsfähigkeit erreichen. KI-Systeme analysieren kontinuierlich riesige Datenmengen aus verschiedenen Quellen, um Muster zu erkennen, Vorhersagen zu treffen und autonome Entscheidungen zu ermöglichen.
Ein zentraler Aspekt der KI-gestützten Prozessoptimierung ist die Fähigkeit, Echtzeitanpassungen vorzunehmen. Traditionelle Produktionslinien waren oft starr und unflexibel. Mit KI können Fertigungsstraßen dynamisch auf veränderte Bedingungen reagieren, sei es Nachfrageschwankungen, Materialengpässe oder Qualitätsprobleme. Diese Agilität ermöglicht es Unternehmen, schneller auf Marktveränderungen zu reagieren und Ressourcen effizienter zu nutzen.
Die Implementierung von KI in der Großproduktion erfordert jedoch eine sorgfältige Planung und Integration. Es ist entscheidend, dass Unternehmen eine klare Strategie entwickeln, die ihre spezifischen Herausforderungen und Ziele berücksichtigt. Welche Prozesse haben das größte Optimierungspotenzial? Wie können Datensysteme konsolidiert werden, um eine umfassende Analyse zu ermöglichen? Diese Fragen müssen beantwortet werden, bevor eine effektive KI-Lösung implementiert werden kann.
Maschinelles Lernen für Predictive Maintenance
Eine der revolutionärsten Anwendungen von KI in der Großproduktion ist Predictive Maintenance. Diese Technologie nutzt maschinelles Lernen, um potenzielle Ausfälle und Wartungsbedarf vorherzusagen, bevor sie auftreten. Dadurch können ungeplante Stillstandzeiten minimiert und die Lebensdauer von Maschinen verlängert werden.
Implementierung von Random Forest Algorithmen
Random Forest Algorithmen haben sich als besonders effektiv für Predictive Maintenance erwiesen. Diese Ensemble-Lernmethode kombiniert mehrere Entscheidungsbäume, um robuste Vorhersagen zu treffen. In der Praxis analysieren Random Forest Modelle historische Daten von Sensoren, Wartungsprotokollen und Leistungsmetriken, um Muster zu identifizieren, die auf bevorstehende Ausfälle hindeuten.
Die Implementierung von Random Forest Algorithmen erfordert eine sorgfältige Auswahl relevanter Merkmale und eine gründliche Datenaufbereitung. Unternehmen müssen sicherstellen, dass ihre Datensätze umfassend und repräsentativ sind, um zuverlässige Vorhersagen zu ermöglichen. Ein gut trainiertes Random Forest Modell kann die Wartungseffizienz um bis zu 30% steigern und ungeplante Ausfallzeiten um bis zu 45% reduzieren.
Einsatz von Long Short-Term Memory (LSTM) Netzwerken
Für komplexere Vorhersageaufgaben, insbesondere wenn zeitliche Abhängigkeiten eine Rolle spielen, kommen oft Long Short-Term Memory (LSTM) Netzwerke zum Einsatz. Diese spezielle Form rekurrenter neuronaler Netze ist in der Lage, langfristige Abhängigkeiten in Zeitreihendaten zu erfassen und zu modellieren.
LSTM-Netzwerke eignen sich besonders für die Analyse von Sensordaten mit komplexen zeitlichen Mustern. Sie können subtile Veränderungen in Vibrations-, Temperatur- oder Druckprofilen erkennen, die auf sich anbahnende Probleme hindeuten. Die Implementierung von LSTM-Modellen erfordert zwar eine größere Datenmenge und Rechenleistung, bietet aber oft genauere Vorhersagen für komplexe Systeme.
Integration von IoT-Sensordaten mit IBM Watson
Die effektive Nutzung von Predictive Maintenance hängt stark von der Qualität und Quantität der verfügbaren Daten ab. Hier kommt das Internet der Dinge (IoT) ins Spiel. Durch die Integration von IoT-Sensoren in Produktionsanlagen können Unternehmen kontinuierlich Echtzeitdaten über den Zustand ihrer Maschinen sammeln.
IBM Watson bietet eine leistungsfähige Plattform für die Integration und Analyse dieser IoT-Daten. Mit Watson können Unternehmen riesige Datenmengen verarbeiten, komplexe Muster erkennen und präzise Vorhersagen treffen. Die Kombination von IoT-Sensoren und Watson's KI-Fähigkeiten ermöglicht eine ganzheitliche Überwachung der Produktionsanlage und eine proaktive Wartungsstrategie.
Anomalieerkennung mittels Autoencodern
Autoencoder, eine spezielle Form neuronaler Netzwerke, haben sich als äußerst effektiv für die Erkennung von Anomalien in Produktionsprozessen erwiesen. Diese Modelle lernen, die normalen Betriebszustände von Maschinen zu codieren und können somit Abweichungen vom Normalzustand schnell identifizieren.
Die Implementierung von Autoencodern für die Anomalieerkennung bietet den Vorteil, dass sie auch bei komplexen, hochdimensionalen Datensätzen effektiv arbeiten können. Sie können subtile Abweichungen erkennen, die menschlichen Beobachtern oder einfacheren statistischen Methoden entgehen würden. In der Praxis hat der Einsatz von Autoencodern zur Anomalieerkennung zu einer Reduktion von Fehlalarmen um bis zu 60% und einer Verbesserung der Früherkennungsrate von Ausfällen um bis zu 40% geführt.
Predictive Maintenance ist nicht nur eine technologische Verbesserung, sondern ein fundamentaler Wandel in der Art und Weise, wie wir über Wartung und Anlagenverfügbarkeit denken. Es verschiebt den Fokus von reaktiver zu proaktiver Instandhaltung und ermöglicht eine nie dagewesene Kontrolle über den Produktionsprozess.
Digitale Zwillinge zur Prozesssimulation
Digitale Zwillinge repräsentieren einen der innovativsten Ansätze in der modernen Fertigungstechnologie. Diese virtuellen Repliken physischer Systeme ermöglichen es Unternehmen, Produktionsprozesse in Echtzeit zu simulieren, zu optimieren und vorherzusagen. Durch die Kombination von IoT-Sensordaten, KI-Algorithmen und 3D-Modellierung bieten digitale Zwillinge eine bisher unerreichte Tiefe an Einblicken und Kontrolle über komplexe Fertigungsumgebungen.
Siemens Tecnomatix Plant Simulation Software
Die Siemens Tecnomatix Plant Simulation Software ist ein führendes Tool für die Erstellung und Nutzung digitaler Zwillinge in der Großproduktion. Diese Plattform ermöglicht es Ingenieuren, detaillierte virtuelle Modelle ihrer Produktionsanlagen zu erstellen und verschiedene Szenarien zu simulieren.
Mit Tecnomatix können Unternehmen:
- Produktionsabläufe optimieren, bevor sie implementiert werden
- Engpässe und Ineffizienzen in bestehenden Prozessen identifizieren
- Die Auswirkungen von Änderungen in der Anlagenkonfiguration vorhersagen
- Energie- und Ressourcenverbrauch minimieren
- Produktionskapazitäten präzise planen
Die Integration von KI-Algorithmen in Tecnomatix ermöglicht es, aus den Simulationsdaten zu lernen und kontinuierlich verbesserte Lösungen vorzuschlagen. Unternehmen, die Tecnomatix einsetzen, berichten von Effizienzsteigerungen von bis zu 20% und einer Reduzierung der Zeit für die Markteinführung neuer Produkte um bis zu 30%.
Echtzeit-Optimierung mit NVIDIA Omniverse
NVIDIA Omniverse bringt die Konzepte der digitalen Zwillinge und der Echtzeit-Kollaboration auf eine neue Ebene. Diese Plattform ermöglicht es Teams, in einer gemeinsamen virtuellen Umgebung an komplexen 3D-Projekten zu arbeiten, einschließlich der Simulation und Optimierung von Produktionsprozessen.
Omniverse nutzt die Leistung von NVIDIA's GPU-Technologie, um hochkomplexe Simulationen in Echtzeit durchzuführen. Dies ermöglicht es Ingenieuren, die Auswirkungen von Änderungen sofort zu sehen und zu bewerten. Die Plattform unterstützt auch die Integration von KI-Modellen, die automatisch Optimierungsvorschläge generieren können.
Ein besonders innovativer Aspekt von Omniverse ist die Fähigkeit, physikbasierte Simulationen durchzuführen. Dies bedeutet, dass die virtuellen Modelle nicht nur visuell genau sind, sondern auch das physikalische Verhalten der realen Welt präzise nachahmen. Diese Genauigkeit ist entscheidend für die Entwicklung und Optimierung von Fertigungsprozessen, insbesondere in Branchen mit strengen Toleranzen wie der Luft- und Raumfahrt oder der Präzisionsmechanik.
Virtual Commissioning mit Emulate3D
Virtual Commissioning, die Praxis, Produktionssysteme in einer virtuellen Umgebung zu testen und in Betrieb zu nehmen, bevor sie physisch implementiert werden, gewinnt zunehmend an Bedeutung. Emulate3D von Rockwell Automation ist eine führende Lösung in diesem Bereich, die es Unternehmen ermöglicht, Risiken zu minimieren und die Zeit bis zur Markteinführung zu verkürzen.
Mit Emulate3D können Ingenieure:
- Komplexe Automatisierungssysteme virtuell testen und debuggen
- Steuerungssoftware validieren, ohne physische Hardware zu gefährden
- Verschiedene Betriebsszenarien simulieren und optimieren
- Schulungen für Bediener in einer sicheren, virtuellen Umgebung durchführen
Die Integration von KI in Emulate3D ermöglicht es, automatisch optimale Konfigurationen und Betriebsparameter zu finden. Unternehmen, die Virtual Commissioning einsetzen, berichten von einer Reduzierung der Inbetriebnahmezeit um bis zu 50% und einer signifikanten Verringerung von Fehlern und Nachbesserungen.
Digitale Zwillinge sind mehr als nur ein technologisches Werkzeug – sie repräsentieren einen fundamentalen Wandel in der Art und Weise, wie wir Produktionssysteme entwerfen, implementieren und betreiben. Sie ermöglichen eine beispiellose Agilität und Präzision in der Fertigungsindustrie.
KI-basierte Qualitätskontrolle in der Fertigung
Die Qualitätskontrolle ist ein kritischer Aspekt jeder Großproduktion, der traditionell zeit- und ressourcenintensiv war. KI-gestützte Systeme revolutionieren diesen Bereich, indem sie eine schnellere, genauere und konsistentere Qualitätsprüfung ermöglichen. Durch den Einsatz von Computer Vision und Deep Learning können selbst kleinste Defekte erkannt werden, die dem menschlichen Auge entgehen würden.
Computer Vision mit TensorFlow und OpenCV
TensorFlow, das Open-Source-Framework für maschinelles Lernen von Google, in Kombination mit OpenCV, einer leistungsstarken Bibliothek für Bildverarbeitung, bildet die Grundlage vieler moderner Computer-Vision-Systeme in der Qualitätskontrolle.
Diese Technologien ermöglichen es, komplexe visuelle Inspektionsaufgaben zu automatisieren. Ein typischer Workflow könnte wie folgt aussehen:
- Erfassung von Bildern oder Videos des zu prüfenden Produkts
- Vorverarbeitung der Bilder zur Rauschunterdrückung und Kontrastverstärkung
- Anwendung von Deep-Learning-Modellen zur Erkennung von Anomalien oder Defekten
- Klassifizierung der erkannten Probleme und Entscheidung über Akzeptanz oder Ablehnung
- Feedback an das Produktionssystem zur kontinuierlichen Verbesserung
Die Implementierung solcher Systeme hat in vielen Fällen zu einer Steigerung der Erkennungsrate von Defekten um bis zu 90% geführt, bei gleichzeitiger Reduzierung der Falsch-Positiv-Rate um bis zu 50%.
Defekterkennung durch Convolutional Neural Networks
Convolutional Neural Networks (CNNs) haben sich als besonders effektiv für die Erkennung visueller Muster und Anomalien erwiesen. Sie sind in der Lage, feine Details und Texturen zu erkennen, die für die Qualitätskontrolle in der Großproduktion entscheidend sind. Die Architektur von CNNs, mit ihren Faltungs- und Pooling-Schichten, ist besonders gut geeignet, um relevante Merkmale aus Bildern zu extrahieren und zu klassifizieren.
Ein typischer CNN-basierter Workflow für die Defekterkennung könnte wie folgt aussehen:
- Vorverarbeitung der Bilder, um Rauschen zu reduzieren und Kontraste zu verstärken
- Durchlaufen des Bildes durch mehrere Faltungsschichten zur Merkmalsextraktion
- Anwendung von Pooling-Schichten zur Dimensionsreduktion und Hervorhebung wichtiger Merkmale
- Durchlaufen vollständig verbundener Schichten zur Klassifikation der extrahierten Merkmale
- Ausgabe einer Wahrscheinlichkeit für das Vorhandensein von Defekten
CNNs haben in vielen Branchen zu dramatischen Verbesserungen in der Qualitätskontrolle geführt. In der Halbleiterindustrie beispielsweise konnten durch den Einsatz von CNNs die Erkennungsraten von Wafer-Defekten um bis zu 95% gesteigert werden, bei gleichzeitiger Reduzierung der Falsch-Positiv-Rate um mehr als 70%.
Echtzeitanalyse mit Edge Computing und NVIDIA Jetson
Die Implementierung von KI-basierter Qualitätskontrolle in Echtzeit stellt hohe Anforderungen an die Rechenleistung und Latenz. Edge Computing, insbesondere mit leistungsstarken Plattformen wie NVIDIA Jetson, bietet hier eine Lösung. Durch die Verarbeitung der Daten direkt am Ort ihrer Entstehung können Entscheidungen in Millisekunden getroffen werden, ohne dass Daten erst an ein zentrales Rechenzentrum übertragen werden müssen.
NVIDIA Jetson-Module bieten:
- Hohe Rechenleistung für KI-Inferenz direkt in der Produktionslinie
- Niedriger Stromverbrauch für effizienten Dauerbetrieb
- Kompakte Bauweise für einfache Integration in bestehende Systeme
- Unterstützung für gängige KI-Frameworks wie TensorFlow und PyTorch
Der Einsatz von Edge Computing mit NVIDIA Jetson hat in vielen Fällen zu einer Reduzierung der Latenz bei der Qualitätskontrolle um bis zu 90% geführt, was eine echte Echtzeit-Analyse und sofortige Korrekturmaßnahmen ermöglicht.
KI-basierte Qualitätskontrolle ist nicht nur eine technologische Verbesserung, sondern ein Paradigmenwechsel in der Fertigungsindustrie. Sie ermöglicht eine Präzision und Konsistenz, die mit menschlichen Prüfern allein nicht erreichbar wäre, und öffnet die Tür zu neuen Levels von Produktqualität und Kundenzufriedenheit.
Optimierung der Lieferkette durch KI
Die Optimierung der Lieferkette ist ein kritischer Faktor für den Erfolg in der Großproduktion. KI-Technologien bieten hier enorme Potenziale, von der Verbesserung der Bedarfsprognose bis hin zur Optimierung von Logistikrouten und der Erhöhung der Transparenz in komplexen globalen Liefernetzwerken.
Bedarfsprognose mit Prophet von Facebook
Prophet, ein Open-Source-Tool von Facebook, hat sich als leistungsfähige Lösung für die Bedarfsprognose erwiesen. Es kombiniert traditionelle statistische Methoden mit maschinellem Lernen, um präzise Vorhersagen zu treffen, selbst bei saisonalen Daten oder Zeitreihen mit vielen fehlenden Werten.
Einige Vorteile von Prophet für die Bedarfsprognose sind:
- Automatische Erkennung von Trends und Saisonalitäten
- Robustheit gegenüber Ausreißern und fehlenden Daten
- Einfache Integration von Geschäftswissen durch manuelle Anpassungen
- Skalierbarkeit für große Datenmengen und viele Produkte
Unternehmen, die Prophet für ihre Bedarfsprognose einsetzen, berichten von einer Verbesserung der Prognosegenauigkeit um bis zu 30% und einer Reduzierung von Überbeständen um bis zu 25%.
Routenoptimierung mittels genetischer Algorithmen
Die Optimierung von Transportrouten ist ein klassisches NP-schweres Problem, für das genetische Algorithmen besonders gut geeignet sind. Diese KI-Technik, inspiriert von der biologischen Evolution, kann komplexe Routenplanungsprobleme effizient lösen und dabei multiple Faktoren wie Entfernung, Verkehr, Lieferfristen und Fahrzeugkapazitäten berücksichtigen.
Ein typischer Ablauf eines genetischen Algorithmus für die Routenoptimierung könnte wie folgt aussehen:
- Generierung einer initialen Population von Routenplänen
- Bewertung jedes Plans anhand einer Fitnessfunktion (z.B. Gesamtkosten)
- Selektion der besten Pläne für die nächste Generation
- Anwendung von Kreuzungs- und Mutationsoperatoren zur Erzeugung neuer Pläne
- Wiederholung der Schritte 2-4 über mehrere Generationen
Der Einsatz genetischer Algorithmen zur Routenoptimierung hat in vielen Fällen zu einer Reduzierung der Transportkosten um 10-20% geführt, bei gleichzeitiger Verbesserung der Liefertreue und Kundenzufriedenheit.
Blockchain-Integration für Rückverfolgbarkeit
Die Integration von Blockchain-Technologie in die Lieferkette bietet eine revolutionäre Möglichkeit, Transparenz und Rückverfolgbarkeit zu gewährleisten. Durch die unveränderliche und dezentrale Natur von Blockchain-Ledgern können alle Transaktionen und Bewegungen in der Lieferkette fälschungssicher dokumentiert werden.
Vorteile der Blockchain-Integration in der Lieferkette:
- Lückenlose Rückverfolgbarkeit von Rohstoffen bis zum Endprodukt
- Reduzierung von Fälschungen und Betrug
- Automatisierung von Verträgen und Zahlungen durch Smart Contracts
- Erhöhte Transparenz für Kunden und Regulierungsbehörden
Unternehmen, die Blockchain in ihre Lieferkette integriert haben, berichten von einer Reduzierung der Zeit für die Rückverfolgung von Produkten um bis zu 80% und einer signifikanten Verbesserung des Vertrauens zwischen Lieferkettenpartnern.
Mensch-Maschine-Kollaboration mit KI
Die erfolgreiche Integration von KI in die Großproduktion hängt nicht nur von der Technologie selbst ab, sondern auch von der effektiven Zusammenarbeit zwischen Mensch und Maschine. KI-Systeme können menschliche Fähigkeiten ergänzen und verstärken, was zu einer Symbiose führt, die die Stärken beider Seiten maximiert.
Cobots mit KI-gestützter Bewegungsplanung
Kollaborative Roboter, oder Cobots, sind darauf ausgelegt, sicher neben Menschen zu arbeiten. Durch die Integration von KI in die Bewegungsplanung dieser Roboter können sie noch adaptiver und effizienter werden. KI-Algorithmen ermöglichen es Cobots, ihre Umgebung in Echtzeit wahrzunehmen und ihre Bewegungen entsprechend anzupassen.
Fortschrittliche KI-gestützte Bewegungsplanung für Cobots umfasst:
- Dynamische Pfadplanung zur Vermeidung von Kollisionen mit Menschen oder Objekten
- Erlernen neuer Bewegungsmuster durch Demonstration oder Reinforcement Learning
- Vorhersage menschlicher Bewegungen zur proaktiven Anpassung
- Optimierung von Bewegungsabläufen für höhere Effizienz und geringeren Energieverbrauch
Der Einsatz von KI-gestützten Cobots hat in vielen Produktionsumgebungen zu einer Steigerung der Produktivität um bis zu 25% geführt, bei gleichzeitiger Verbesserung der Arbeitssicherheit und Reduzierung der körperlichen Belastung für menschliche Arbeiter.
Augmented Reality für Wartung mit Microsoft HoloLens
Augmented Reality (AR) Technologien wie Microsoft HoloLens revolutionieren die Art und Weise, wie Wartungs- und Reparaturarbeiten in der Großproduktion durchgeführt werden. Durch die Überlagerung digitaler Informationen auf die reale Umgebung können Techniker komplexe Aufgaben effizienter und präziser ausführen.
Einige Anwendungsfälle für AR in der Wartung sind:
- Schritt-für-Schritt-Anleitungen, die direkt im Sichtfeld des Technikers eingeblendet werden
- Remote-Unterstützung durch Experten, die das Sichtfeld des Technikers in Echtzeit sehen können
- Visualisierung von Sensordaten und Diagnoseinformationen direkt an der Maschine
- Virtuelle Simulationen von Wartungsprozeduren für Trainingszwecke
Unternehmen, die AR-Technologien wie HoloLens in ihre Wartungsprozesse integriert haben, berichten von einer Reduzierung der Wartungszeiten um bis zu 40% und einer Verbesserung der Genauigkeit bei komplexen Reparaturen um bis zu 90%.
Natural Language Processing für Sprachsteuerung in der Produktion
Natural Language Processing (NLP) ermöglicht es, Maschinen und Systeme in der Produktion durch natürliche Sprache zu steuern. Dies verbessert nicht nur die Ergonomie und Benutzerfreundlichkeit, sondern ermöglicht auch eine effizientere Interaktion zwischen Mensch und Maschine, insbesondere in Umgebungen, wo die Verwendung von Tastaturen oder Touchscreens unpraktisch ist.
Anwendungsbeispiele für NLP in der Produktion umfassen:
- Sprachgesteuerte Bedienung von Maschinen und Robotern
- Automatische Erstellung von Produktionsberichten durch Sprachdiktate
- Intelligente Assistenzsysteme, die auf Sprachbefehle reagieren und kontextbezogene Informationen liefern
- Übersetzung von Anweisungen in Echtzeit für multinationale Produktionsteams
Die Integration von NLP-Technologien in Produktionsumgebungen hat in vielen Fällen zu einer Steigerung der Produktivität um bis zu 15% geführt, insbesondere in Bereichen, wo Hände-frei-Bedienung kritisch ist.